28. September 2022
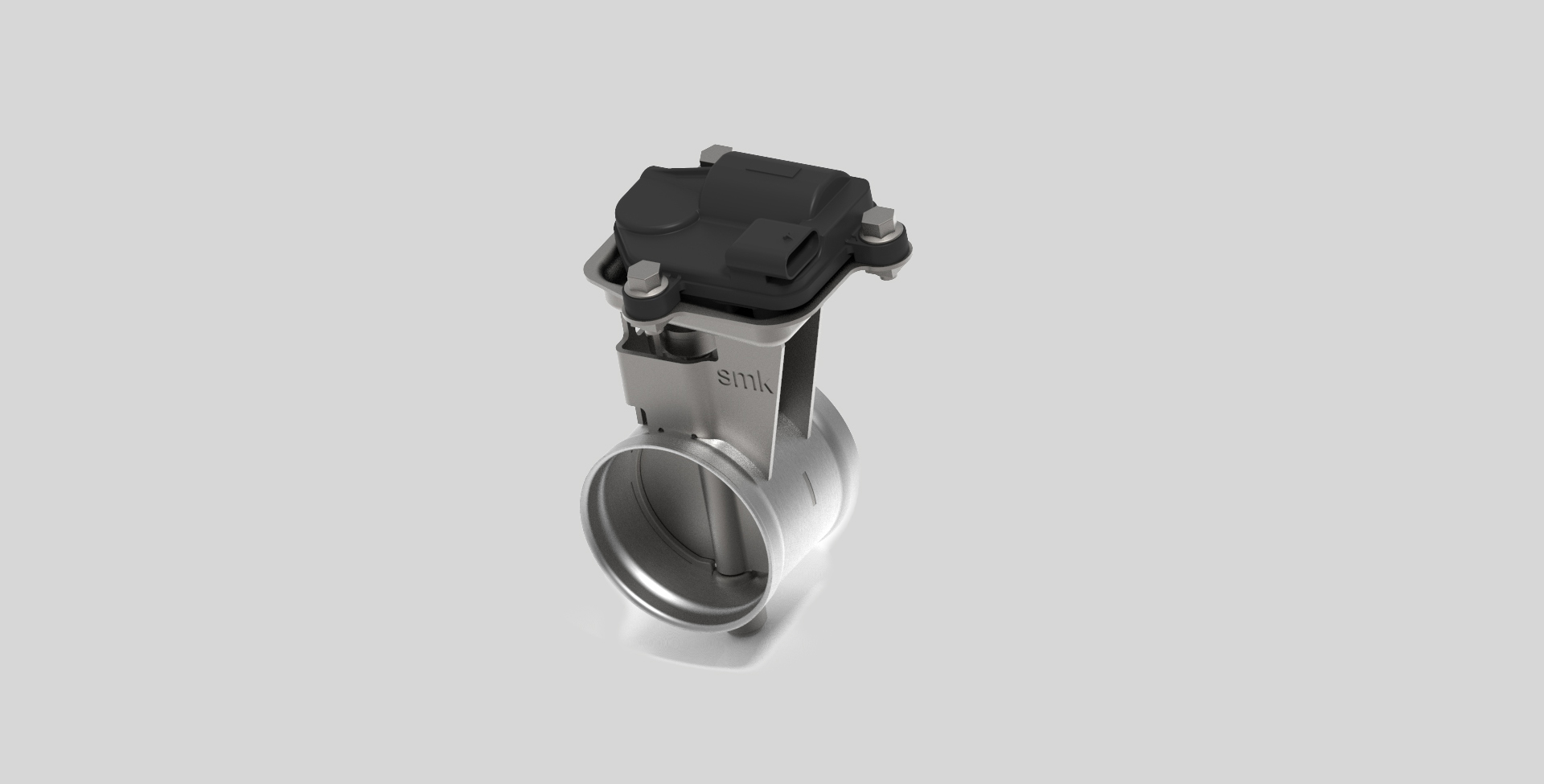
Case Study
Exhaust gas valve Gen3 Lightweight with resource-saving design
The challenge
We have been developing control valves to control exhaust gas flows in vehicles for many years. Our own challenge was to bring the performance of the exhaust flaps to a new level. Particular attention was paid to internal and external leakage and reduced heat input in the electric actuators while reducing weight and cost.
The smk solution
The new generation of smk exhaust flaps has a deep-drawn valve housing that uses less material, requires less welding and eliminates the need for machining. To optimise the manufacturing process, all individual parts are positioned using a twist-proof plug-in system.
The successful result
Challenge fulfilled: We achieved a material saving of 50 % and were able to significantly improve both the internal/external leakage and the acoustic tightness. Since then, of course, our customers have also benefited from the cost savings.
We would be happy to advise you in a personal meeting.
Just get in touch with us!